The ruggedbot or short rugbot type of robot is an in-house development for Safety, Search, and Rescue Robotics based on the CubeSystem, a collection of hardware and software components for fast robot prototyping. Rugbots are tracked vehicles that are lightweight (about 35 kg) and have a small footprint (approximately 50 cm x 50 cm). They are very agile and fast on open terrain. An active flipper mechanism allows Rugbots to negotiate stairs and rubble piles.
Their small footprint is highly beneficial in indoor scenarios. They have significant on-board computation power and they can be equipped with a large variety of sensors. The standard payload includes a laser-scanner, ultrasound sensors, four cameras, one thermo camera, and rate gyros. The onboard software is capable of mapping, detection of humans and fully autonomous control. Teleoperation is in varying degrees is also supported. The on-board batteries allow for 2.5 to 3 hours of continuous operation.
Work on the rugbots started in 2004. Rugbots have been used in several SSRR competitions and field trials including the RoboCup German Open 2005 in Paderborn Germany and the RoboCup worldchampionship 2005 in Osaka Japan.
Locomotion
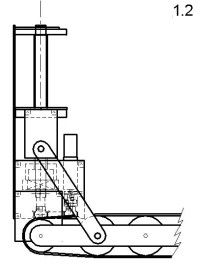
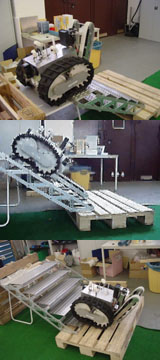
Rugbots like many other robots designed for operation in rough environments use tracks. This type of locomotion is often considered as the most versatile locomotion system as it can handle relatively large obstacles and loose soil. The technology for tracked locomotion is well understood and simple. The positive points are smooth locomotion on relatively smooth terrain, superb traction on loose ground, the ability to handle large obstacles as well as small holes and ditches, as well as a good payload capacity. For the negative points, there is slip friction when the vehicle must turn. Also, if the locomotion has only one pair of belts, it will suffer from impacts, e.g. when climbing over large boulders 2 or when it starts going down steep slopes. Nevertheless, tracked locomotion is the most suitable to surmount obstacles, negotiate stairways, and it is able to adapt to terrain variations.
There is no ideal footprint for a mobile robot. In some situations, for example when climbing up a rubble pile or stairs, the footprint has to be large to maximize traction and to prevent tilting over. In other situations, for example when moving through narrow passages or through doorways, the footprint has to be small to prevent to get stuck. The common approach is to use flippers, i.e., additional support tracks that can change their posture relative to the main locomotion tracks. For rugbots a novel mechatronic design for flippers is used that overcomes a significant drawback in the state of the art approaches, namely the large forces in the joint between main locomotion tracks and flippers. Instead of directly driving this joint to change the posture, a link mechanism driven by a ballscrew is used.
A differential drive based on two tracks is simple and in principle already very capable, but there is a significant problem especially for robots operating in rough environments. A critical aspect is that it is almost impossible to select the right parameters for a single pair of tracks. For some situations, for example when negotiating narrow passages, the footprint of the robot and hence the length of the tracks should be small. When climbing large obstacles, slopes or stairs the footprint should be large. The common solution to this problem is to use additional tracks that can change their posture relative to the main robot body. The state of the art for changing the posture of the flipper is to directly drive the joint between the additional small track and the main locomotion system. This approach has the tremendous disadvantage that due to the large forces on this active joint it is extremely difficult to construct mechanisms that are sufficiently stable and still within feasible size and weight limits.
So the standard approach to change the posture of a flipper is to directly drive the joint. This can be done by spur or worm gear or a belt or chain drive. But no matter what mechanism is used, it has to take quite some stress. First of all, it has to provide high forces for moving the flipper under load, especially for pushing it down when the full weight of the robot is supported by it. Second, it is subject to shocks and impacts, for example when the robot drives over bumps, stairs, etc. Especially these forces can be very high and they are very hard to predict. It is hence almost impossible to design a fail-safe mechanism within feasible weight and size limits with this approach. Accordingly, broken flipper joints are a common problem.
The novel flipper design of rugbot consists of a ball screw, a passive link and a motor. The driving force that needs to be provided by the motor is smaller with this set-up. Furthermore, all shocks go against the passive link and the ball screw, which in contrast to spur/worm-gears or belt/chain-drives can be easily laid out to absorb them without any damage.
Sensors and Onboard Intelligence
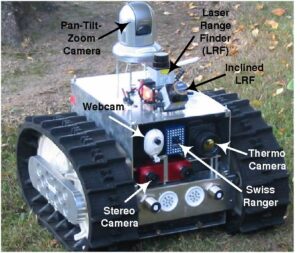
The rugbots have significant onboard computation power and various sensor payloads. They can be teleoperated or even run fully autonomous missions in challenging domains like Search and Rescue (SAR). The development of intelligent behaviors is in addition to the robots’ mechatronics a great challenge in this research area.
The robot must for example autonomously detect victims and hazards. Special sensors like CO2 detectors and Infrared cameras are used to detect humans. Within the thermo images, a special approach is for example used to detect human shapes.
The onboard software of rugbots also covers mapping, exploration and planning. Related research includes 3D mapping in unstructured environments. Last but not least, the onboard software enables rugbots to cooperate in multi-robot-teams.